Third Party Safety Audit (IS: 14489)
A Third Party Safety Audit conducted under IS 14489:1998 is a systematic, independent evaluation of an organization's Occupational Safety and Health (OSH) systems. This audit, performed by external experts, assesses the effectiveness of safety policies, procedures, and practices, ensuring compliance with legal and regulatory standards. The process involves reviewing documentation, inspecting workplace conditions, and evaluating employee adherence to safety protocols. By identifying potential hazards and recommending corrective actions, the
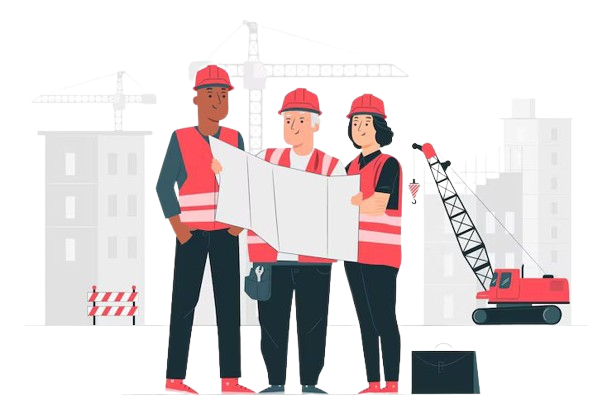
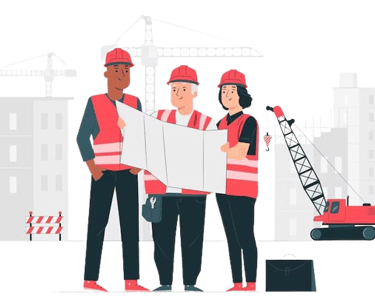
Main Purpose of Third Party Safety Audit (IS: 14489)
Ensure Compliance with Regulations: Verify that the organization adheres to applicable occupational safety and health laws, standards, and internal policies.
Identify Potential Hazards: Systematically detect unsafe conditions, practices, or processes that could lead to accidents or incidents.
Evaluate Safety Management Systems: Assess the effectiveness of existing safety protocols and procedures in achieving defined safety objectives.
Promote Continuous Improvement: Provide recommendations for enhancing safety performance and fostering a proactive safety culture.
Enhance Risk Management: Assist in identifying and mitigating risks, thereby reducing the likelihood of workplace accidents and associated costs.
Facilitate Objective Assessment: Engage independent auditors to provide an unbiased evaluation of the organization's safety practices.
Support Legal and Regulatory Compliance: Help organizations meet statutory requirements, such as those outlined in the Factories Act, 1948, and other relevant regulations.
Improve Emergency Preparedness: Assess the adequacy of emergency response plans and the organization's readiness to handle unforeseen events.
Enhance Employee Awareness: Encourage employee involvement and awareness regarding safety protocols and the importance of maintaining a safe work environment.
Benchmark Safety Performance: Compare current safety practices against industry best practices and standards to identify areas for improvement.
What Does the Audit Cover?
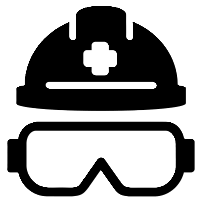
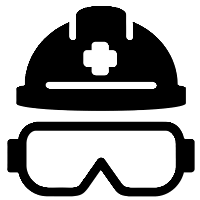
Operational Safety
Inspection of machinery, equipment, and processes.
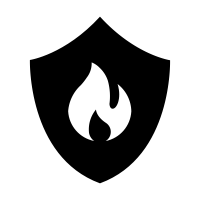
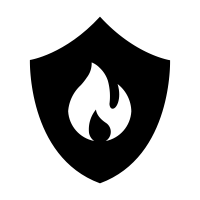
Fire Prevention
Assessment of fire safety systems and emergency preparedness.
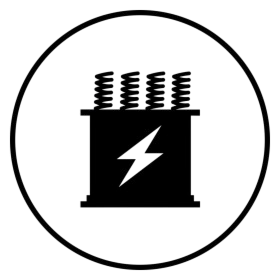
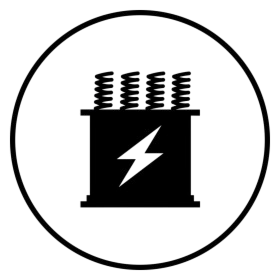
Electrical Systems
Comprehensive checks for electrical safety.
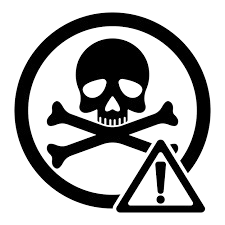
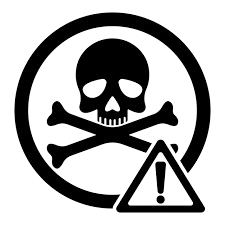
Hazardous Substances
Safe handling, storage, and disposal evaluations.
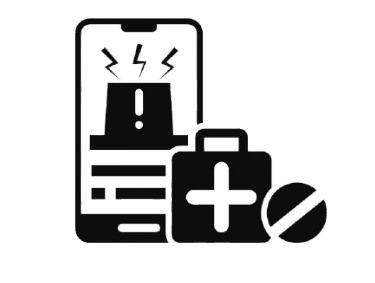
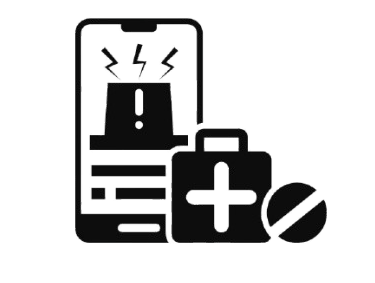
Emergency Readiness
Gauging the effectiveness of emergency response mechanisms.
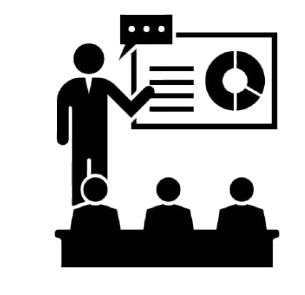
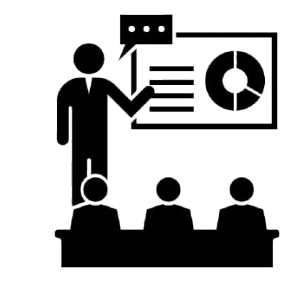
Employee Training
Verification of safety documentation and training programs.
audit aims to enhance workplace safety, prevent accidents, and promote a culture of continuous improvement. Regular third-party audits are crucial for organizations to maintain high safety standards and demonstrate their commitment to employee well-being.
Our Address
5A/3, Ratan Nagar, Teen Dukan, Dehar Ka Balaji, Jaipur, 302039, Rajasthan
greendashindia@gmail.com
+91-8003097697
About Us
Greendash provides consultancy in environment, health, safety, and fire protection, ensuring compliance and sustainability across various industries in India.
Useful Links
Contact...